2025 Kirjoittaja: Howard Calhoun | [email protected]. Viimeksi muokattu: 2025-01-24 13:16
Muottien valua kutsutaan myös kuorivaluksi. Ja ulkomailla tätä työtapaa kutsutaan Shelliksi.
Yleistä tietoa
Nykypäivän teollisuusteollisuudessa käytetään monia erilaisia valumenetelmiä. Vaippavalun lisäksi käytetään myös investointivalua, metallimuoteissa ja useissa muissa menetelmissä. Näiden valumenetelmien kokonaisetu hiekkamuovaukseen verrattuna on, että niillä saadaan tarkempia loppumateriaaleja muodon ja mittojen suhteen. Lisäksi tällaisten tuotteiden pinnan epätasaisuuksien määrä vähenee. Harvemmissa tapauksissa, mutta silti tapahtuu, että myöhemmän koneistuksen tarve sulatuksen jälkeen jää pois. Kaiken lisäksi valun käyttö kuorimuotteissa ja muissa menetelmissä myötävaikuttaa siihen, että tämä prosessi voidaan koneistaa mahdollisimman paljon, minkä seurauksena myös sen automatisointi lisääntyy. Ja tämä tietysti lisää suuresti minkä tahansa teollisuuslaitoksen tuottavuutta.
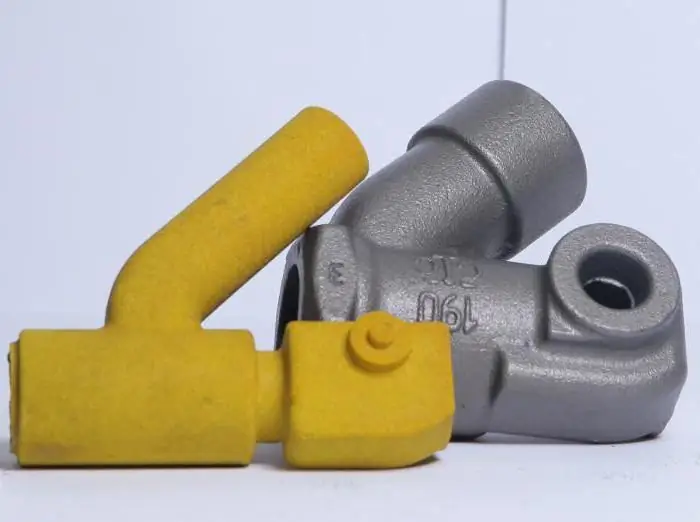
Shell-valu
Jos puhumme nimenomaan tästämenetelmällä, se otettiin ensimmäisen kerran käyttöön tehtailla vuonna 1953. Tällä hetkellä menetelmää käytetään melko laajasti. Suurin osa Kirovets-traktorin osista valmistetaan esimerkiksi valulla kuorimuotteihin. Kaikki tällä menetelmällä valmistetut osat ovat korkealaatuisia teräksestä tai valuraudasta. Vaippavalu on menetelmä, jossa valun lopputulos on kahdesta hiekka-hartsikuoresta koostuva muoto. Myös tätä osien valmistusmenetelmää käytetään vain tapauksissa, joissa on tarpeen luoda pieni tai keskikokoinen osa, mutta samalla erittäin tarkasti. Esimerkkejä tämän valumenetelmän sovelluksista ovat moottorin osat tai ohutseinämävalut.
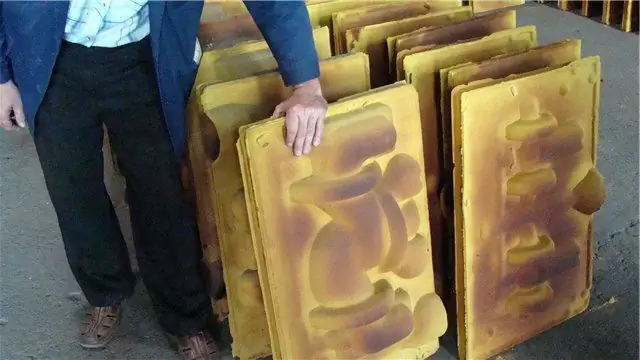
The Essence of the Way
Tällä työmenetelmällä saat erilaisia osia tuulettimiin, moottoreihin, pumppuihin tai tekstiilikoneisiin. Vastaanotetun tuotteen enimmäispituus ei kuitenkaan saa ylittää 1 metriä, eikä se saa olla painavampi kuin 200 kg.
Kuorimuottien valun olemus perustuu tiettyihin lämpökovettuvien hartsien ominaisuuksiin, jotka ovat osa hiekka-hartsiseoksia. Tällaisten komponenttien käytön etuna on, että näillä hartseilla on taipumus kovettua nopeasti ja pysyvästi, kun niitä käsitellään 200-250 celsiusasteen lämpötilassa.
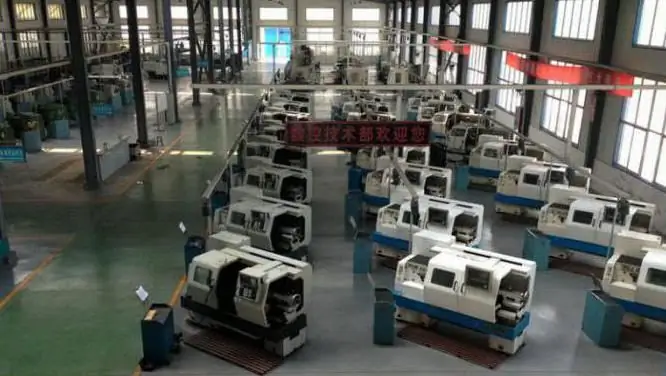
Kuorimuotin tekeminen valua varten
Muotin tekemiseksi myöhempää valua varten tarvitaan hienorakeista kvartsihiekkaa, johon on lisätty lämpökovettuvaa hartsia, joka on sen liitoselementti täysimittaisen kuorimuotin saamiseksi. Nämä materiaalit, erityisesti hartsi, valitaan, koska ne kovettuvat ohittaessaan tietyn lämpötilaesteen. Valmistusprosessi on seuraava. Ensin hartsi kuumennetaan 140-160 celsiusasteeseen. Tällaisen ympäristön vaikutuksesta se muuttuu nestemäiseksi liimamassaksi, joka peittää kvartsihiekkamuotin kokonaan.
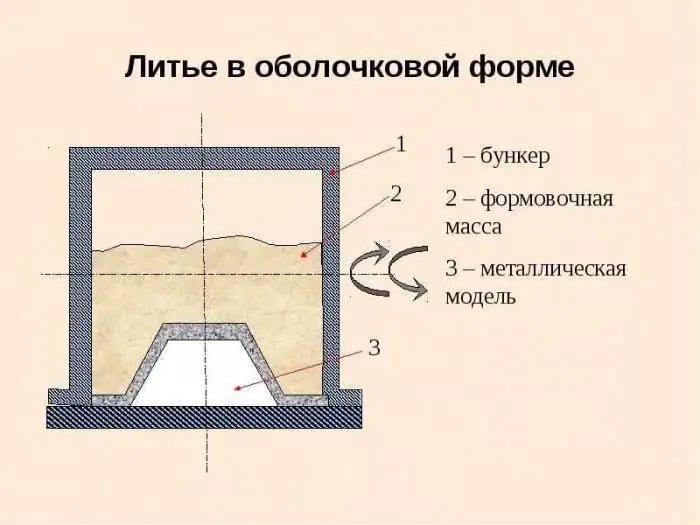
Kuorimuottien valun laajuus on melko laaja, ja siksi muottien valmistusprosessi siirretään automaattiseen tai automatisoituun.
Kun muotti on peitetty kokonaan hartsilla, lämpötila nostetaan 200-250 celsiusasteeseen. Tämä lämpötilakynnys on riittävä, jotta liimamassa kovettuu palautumattomasti ja muodostaa muodon. Lisäksi, kun osien valuprosessi alkaa, eli kun sula metalli tulee muottiin, sen lämpötila saavuttaa noin 600 astetta. Tämä tila riittää varmistamaan, että hartsi ei sula, vaan palaa, jättäen samalla huokoset itse muottiin, mikä helpottaa kaasujen poistumista.
Kuorimuottivalun edut ja haitat
Kuten kaikilla muillakin valmistusmenetelmillä, tälläkin on hyvät ja huonot puolensa. Jos verrataan tätä valumenetelmää esimerkiksi sisäänvaluontavallisissa hiekkamuoteissa on useita etuja:
- Ensimmäinen ja melko merkittävä ero on tarkkuusluokka, joka on 7-9. Lisäksi saadun osan pintakäsittely paranee 3-6:een. Lisäksi vähennetään lisäyksiä, jotka ovat sallittuja syntyvän osan myöhempään työstöön valun jälkeen.
- Yksi suurista eduista on valukappaleiden valmistuksen työvoimakustannusten merkittävä aleneminen.
- Tämä valumenetelmä vähentää valumateriaalien kulutusta sekä metallin määrää, koska porttikanavien koko pienenee.
- Vähentänyt avioliittojen määrää merkittävästi.
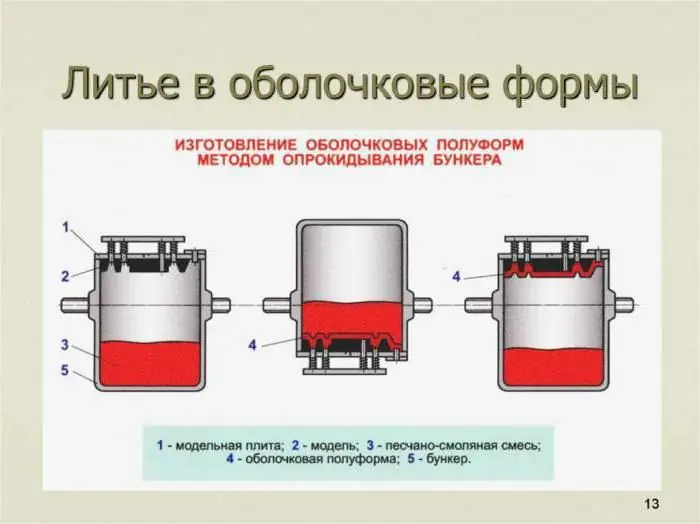
Kuorimuottien valussa on kuitenkin joitain haittoja. Näitä ovat:
- Muotin käyttöikä - 1 valu.
- Muovaushiekan hinta on melko korkea.
- Suuri prosenttiosuus haitallisia kaasuja.
Korpuksenmuodostusprosessi
Kehonmuodostusprosessi suoritetaan kuudessa vaiheessa:
- Ensimmäinen vaihe on prosessi, jossa seos kaadetaan kuumalle metallimallille, sekä prosessi, jossa sitä pidetään useita kymmeniä sekunteja, kunnes osan ympärille muodostuu ohut, vahva kuori. Useimmiten mallit valmistetaan valuraudasta ja niiden lämmitys suoritetaan 230-315 asteeseen asti.
- Sen jälkeen on suoritettava toimenpide ylimääräisen muovaushiekan poistamiseksi. Kuoren paksuuden tulisi lopulta olla 10-20mm. Se riippuu seoksen viipymäajasta mallissa sekä lämpötilasta.
- Sen jälkeen on tarpeen siirtää mallilevy yhdessä muotin kanssa uuniin, jossa ne ovat kovettumisprosessin loppuun asti. Tämän toimenpiteen lopussa vaipan lujuuden tulee olla välillä 2,4 - 3,1 MPa.
- Uunista poistamisen jälkeen kovettunut kuori siirtyy pois levystä. Tätä toimenpidettä varten käytetään erityistä työntölaitetta.
- Sen jälkeen kaksi tai useampi malli kiinnitetään yhteen jollain puristimella tai liimaamalla. Näitä muotteja voidaan käyttää valamiseen kuorimuotteihin tai yksinkertaisesti varastoida. Lähes rajoittamaton säilyvyys.
- Ennen valuprosessin aloittamista valmiissa muotissa, niihin kaadetaan hauli, mikä auttaa estämään tai tuhoamaan muotin myöhemmän kaatamisen aikana.
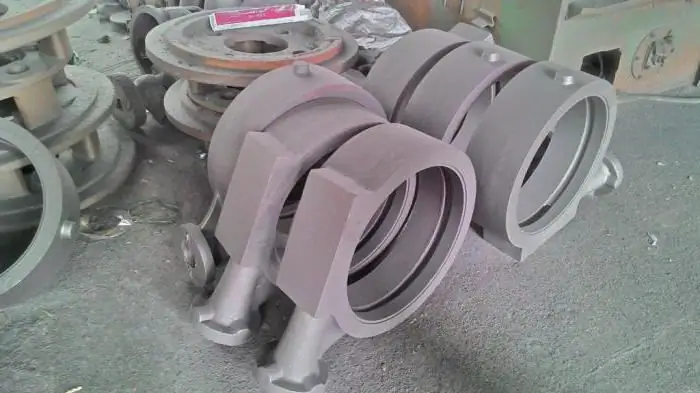
Lähetystiedot
On syytä aloittaa siitä, että tyypilliset työkalujen valmistuksessa sallitut toleranssit voivat olla 0,5 mm. Pinnan karheus on sallittu välillä 0,3 - 0,4 mikronia. Tällaiset rajat ovat perusteltuja sillä, että käytetään hienojakoista hiekkaa. Myös huomionarvoinen: hartsin käyttö myötävaikuttaa suuresti siihen, että pinta on erittäin sileä.
Tuotantomäärät
Tällaisten muottien ja osien valmistukseen osallistumiseksi on huolehdittava muottimallin asennuksesta. Asennusaika on alle viikko. Kun asennus on valmis, ulostulomäärä voisaavuttaa 5-50 kappaletta tunnissa. Tällaiset tuotantomäärät tunnissa ovat melko todellisia, mutta tätä varten on tarpeen valmistella valuprosessi vastaavasti. Tärkeimmät valussa tarvittavat materiaalit ovat valurauta, alumiini, kupari sekä tämäntyyppisten metallien seokset. Toinen välttämätön materiaali on seos, jossa käytetään alumiinia ja magnesiumia.
Suositeltava:
Bensiini "Shell": arvostelut ja tekniset tiedot
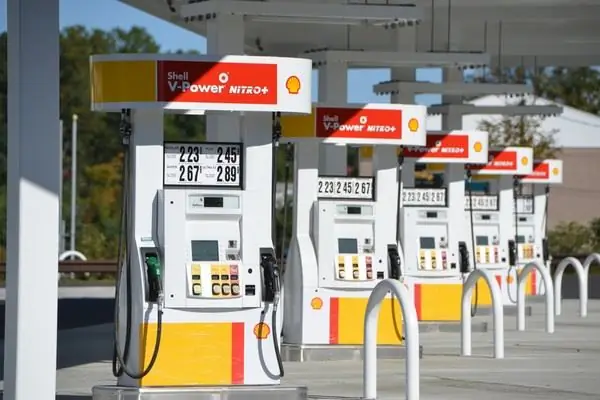
Artikkeli ei ole Shell-tuotteiden mainos, joten ensin määritellään kriteerit hyvälle autopolttoaineelle periaatteessa ja sitten käsitellään Shell-merkkisen bensiinin vivahteita. Autoilijoiden arvostelut Shell-bensiinistä ovat erilaisia ja subjektiivisia. Käsitelkäämme siis rauhallisesti ja ilman tunteita