2025 Kirjoittaja: Howard Calhoun | [email protected]. Viimeksi muokattu: 2025-01-24 13:16
Öljyn hyödylliset ominaisuudet ovat olleet ihmiskunnan tiedossa ammoisista ajoista lähtien. Sitä käytetään polttoaineen ja raaka-aineiden saamiseksi synteettisten kuitujen ja muovien valmistukseen. Samaan aikaan ihmiskunta on aina pyrkinyt maksimoimaan fossiilisten polttoaineiden käsittelystä saatavat hyödyt. Yksi näistä menetelmistä oli katalyyttinen reformointi, prosessi, joka johti korkealaatuisiin bensiineihin ja aromaattisiin hiilivetyihin.
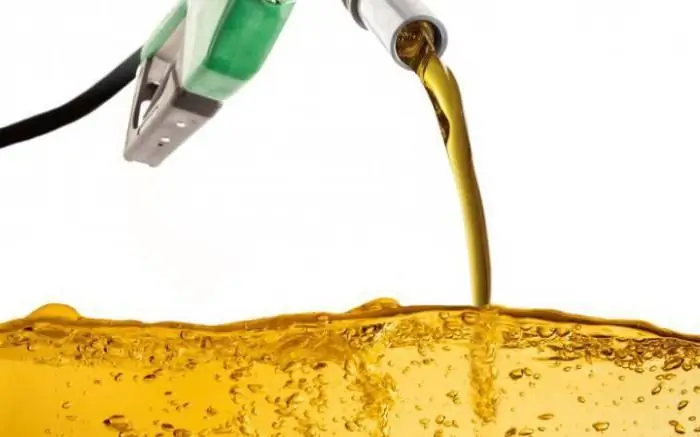
Tämä öljynjalostusmenetelmä keksittiin jo vuonna 1911, ja vuodesta 1939 lähtien tekniikkaa on käytetty teollisessa mittakaavassa. Siitä lähtien fossiilisten polttoaineiden tislausmenetelmää on parannettu jatkuvasti. Nykyään se on yksi monimutkaisimmista ja tehokkaimmista tavoista tuottaa korkeaoktaanista bensiiniä.
Polttoaineen tislaus
Katalyyttinen reformointi on kuusijäsenisten nafteenien dehydrausprosessi (vetymolekyylin poistaminen orgaanisista yhdisteistä) nikkelin ja jonkin verranmuut platinaryhmän metallit korkeassa lämpötilassa, mikä johtaa aromaattisten yhdisteiden muodostumiseen. Toisin sanoen tämä on prosessi, jonka avulla on mahdollista saada korkeaoktaaninen tuote - reformaatti - huonolaatuisista raaka-aineista - suorasyötöksestä bensiinistä.
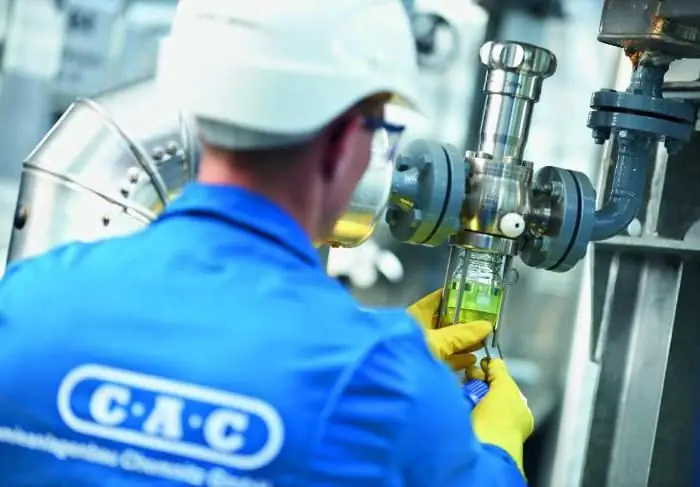
Pääsyy, miksi uudistuksesta on tullut niin laajalle levinnyttä, on huoli ympäristöstä. Ennen tätä korkeaoktaanisen bensiinin valmistukseen käytettiin lyijypohjaisia nakutuksenestoaineita. Lähes ei päästöjä uudistamisesta.
Vastaanotetut tuotteet
Tällä tekniikalla on mahdollista uuttaa arvokkaimmat petrokemian raaka-aineet - bentseeni, tolueeni, aromaattiset hiilivedyt. Nykyään katalyyttinen reformointi on prosessi, joka tuottaa jopa 480 miljoonaa tonnia petrokemian aineita vuodessa maailmanlaajuisesti.
Tuotantosyklin päälopputuote on uudelleenmuotoilu - bensiini, jonka oktaaniluku on 93-102.
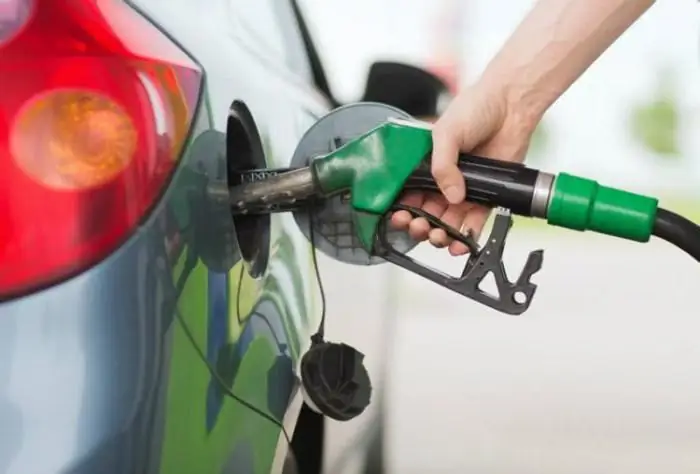
Samaan aikaan syntyy parafiinisia sivutuotteita sekä 90 % vetykaasua, joka on puhtainta kuin muilla menetelmillä saatu.
Toinen katalyyttiseen reformointiin liittyvä tuote on koksi. Se kerrostuu katalyyttien pinnalle, mikä vähentää merkittävästi niiden aktiivisuutta. He yrittävät vähentää sen määrää.
Katalyyttinen reformointitekniikka
Suorakäyntiinen bensiini, matalaoktaaninen polttoaine, toimii katalyyttisen reformoinnin raaka-aineena. Koko prosessi suoritetaan 3-4 reaktorissa, joissa on kiinteä katalyyttipeti. Reaktorit on yhdistetty toisiinsa putkilla, joissa on monimutkainen monikammiojärjestelmä ja siirtymätuotteen lämmitys.
Katalyyttisen reformoinnin katalyytit ovat kantajaa - alumiinioksidia (A1203), johon on sekoitettu platinakiteitä. Reaktoreissa, joiden lämpötila on 480-520 °C ja paine 1,2-4 MPa, raaka-aine muunnetaan korkeaoktaanisiksi isoparafiineiksi ja aromaattisiksi yhdisteiksi.
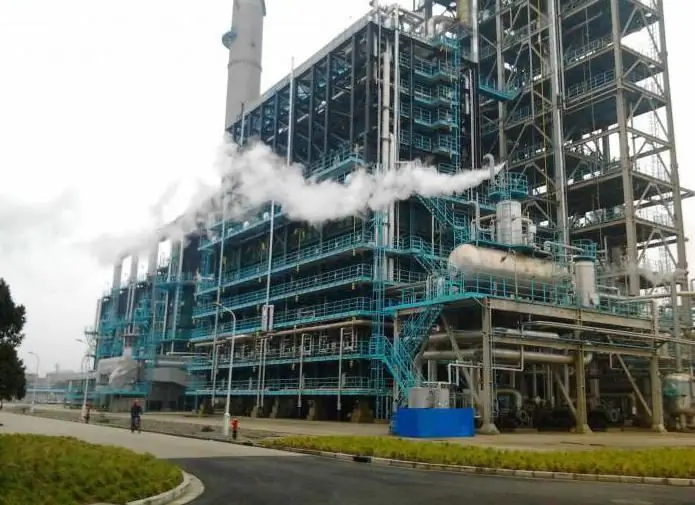
Hyvin usein prosessin vakauden lisäämiseksi teknologiaan tuodaan kalliimpia metalleja (renium, germanium, iridium) sekä halogeeneja - klooria ja fluoria.
Katalyyttisen reformoinnin tyypit
Tähän mennessä on keksitty monia menetelmiä korkeaoktaanisen bensiinin ja aromaattisten hiilivetyjen tuottamiseksi katalyyttisten reformointireaktioiden avulla. Jokainen ulkomainen yritys pitää oman tuotantomenetelmänsä salassa. Ne kuitenkin kaikki perustuvat kolmeen päämenetelmään:
- Öljyreformointi suoritetaan samanaikaisesti kolmessa tai neljässä reaktorissa jatkuvasti. Sen ydin on siinä, että prosessin katalyytti kehittää ensin täysin potentiaalinsa, minkä jälkeen reaktorit pysäytetään, kunnes kiihdytin palauttaa ominaisuudet.
- Jatkuva reaktio 2-3 asennuksessa - reagenssi palautetaan säännöllisesti jokaiseen järjestelmään sitä mukaa kun sitä valmistetaan. Samaan aikaan prosessi ei pysähdy, ja regeneratiivinen reaktori korvataan "kelluvalla", lisäreaktorilla.
SuurinTuottavuus voidaan saavuttaa jatkuvalla reaktiolla regenerointiyksiköiden ja reaktorien avulla. Katalyytti sijoitetaan sen ominaisuuksien huonontuessa regenerointikammioon ja tilalle tulee "äskettäin pelkistetty reagenssi", alumiini-platina-yhdisteiden kierto tapahtuu.
Pääongelma
Pääasiallinen reformointiin liittyvä ongelma on suuren koksin muodostuminen, mikä heikentää alumiinioksidi-platinamateriaalien katalyyttistä kykyä. Ratkaisu tähän ongelmaan on polttaa koksikerrostumat reagoivien elementtien pinnalle hapen suhteen inertillä seoksella lämpötilassa 300-500 celsiusastetta. Tätä tiedeyhteisön prosessia kutsutaan regeneraatioksi.
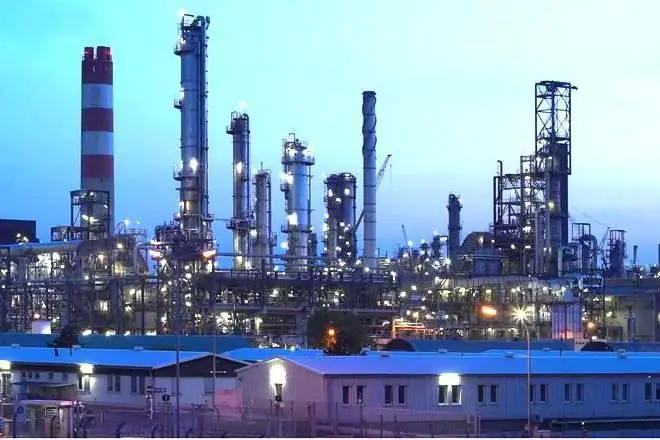
Katalyyttisen elementin palauttaminen kokonaan on mahdotonta. Käytettäessä se vanhenee peruuttamattomasti, minkä jälkeen se lähetetään erikoistehtaille, joissa siitä uutetaan platinaa ja muita kalliita metalleja.
Katalyyttiset uudistajat
Tätä luonnonpolttoaineiden käsittelymenetelmää käytetään erilaisissa laitoksissa. Muutamia niistä mainitakseni:
- Selectoforming. Tässä reformaattorissa yhdistyy katalyyttinen dehydrausprosessi ja selektiivinen vetykrakkaus.
- Alusta. Siinä on 3 reaktoria ja katalyyttien toiminta-aika on 6-12 kuukautta.
- Ultramuotoilu. Yksi ensimmäisistä asennuksista, joissa on "kelluva" reaktori, joka suorittaa reagenssin pelkistysprosessin.
- Isoplus. vartentuotteen saamiseksi yhdistetään reformointi- ja lämpökrakkausprosessit.
Yleisin öljyreformointi on saatu Pohjois-Amerikassa - täällä käsitellään vuosittain jopa 180 miljoonaa tonnia luonnonpolttoainetta. Toisella sijalla ovat Euroopan maat - niiden osuus on noin 93 miljoonaa tonnia. Venäjä sulkee kolmen parhaan vuotuisen öljyntuotannon noin 50 miljoonaa tonnia.
Suositeltava:
Voronežin panimo: suuri yritys, jolla on vuosisadan historia
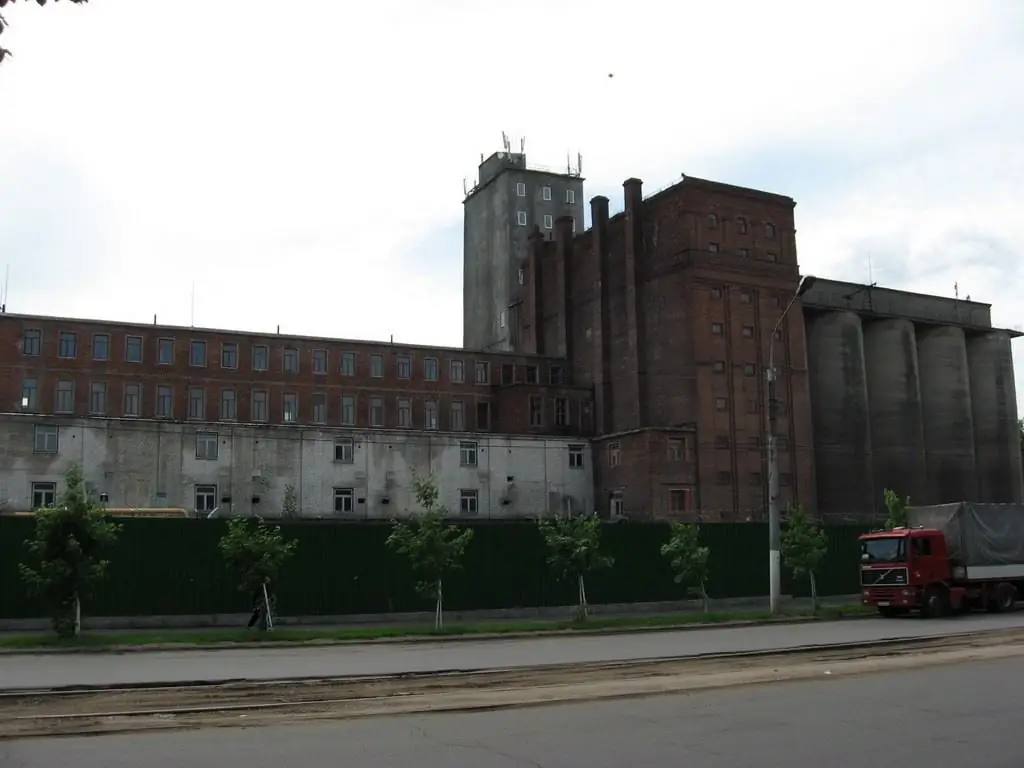
Voronežin panimo on ollut Black Earth -alueen pääkaupungin kartalla jo vuosia. Tämä yritys selvisi Neuvostoliiton noususta teollisuudessa ja jopa perestroikan vaikeista ajoista. Nykyään se on osa mahtavaa olutteollisuutta ja toimittaa tuotteitaan kaikkiin Venäjän kolkoihin
Hyvä pankki, jolla on paras korko talletuksille
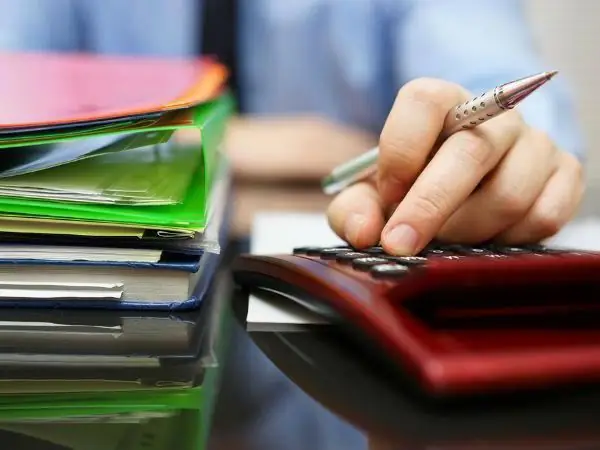
Jokaiselle, jolla on tiettyjä säästöjä ja jotka haluavat lisätä niitä, on tärkeää löytää hyvä pankki, jolla on edulliset talletuskorot. Ottaen huomioon venäläisten pankkien tarjoamat ehdot, on kiinnitettävä huomiota moniin vivahteisiin: ehdot, hinnat, täydennys- tai veloitustapahtumien mahdollisuus, pääoma
Resurssia säästävä tekniikka. Teolliset teknologiat. Uusin tekniikka
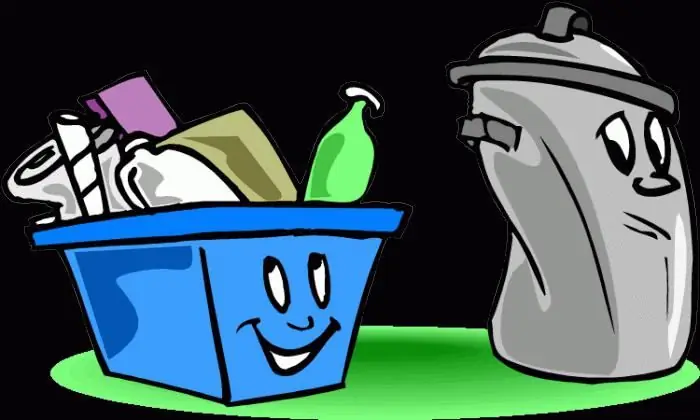
Moderni teollisuus kehittyy erittäin dynaamisesti. Toisin kuin viime vuosina, tämä kehitys etenee intensiivisesti viimeisimmän tieteellisen kehityksen myötä. Resursseja säästävä tekniikka on erittäin tärkeä. Tämä termi viittaa kokonaiseen toimenpidejärjestelmään, jolla pyritään vähentämään merkittävästi resurssien kulutusta säilyttäen samalla tuotteiden korkea laatutaso. Ihannetapauksessa he yrittävät saavuttaa mahdollisimman alhaisen raaka-aineiden kulutuksen
Jeni on japanilainen valuutta, jolla on rikas historia
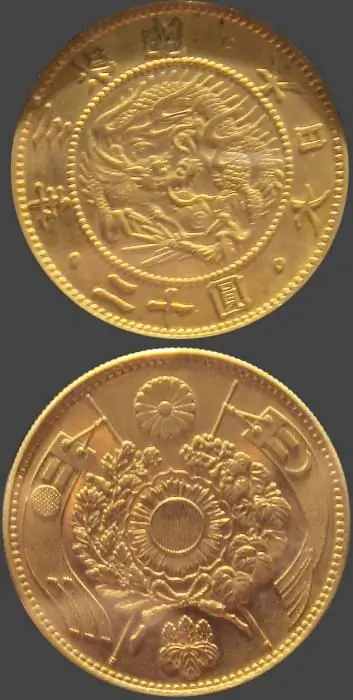
Harvat ihmiset tietävät Japanin valuutan nimen, koska ulkomailla jeni on kolmanneksi suosituin, toiseksi vain Yhdysv altain dollarin ja euron jälkeen. Meijin johtama hallitus otti sen käyttöön vuonna 1872 tavoitteenaan luoda järjestelmä, joka on samanlainen kuin Euroopan
T-54 - säiliö, jolla on pitkä historia
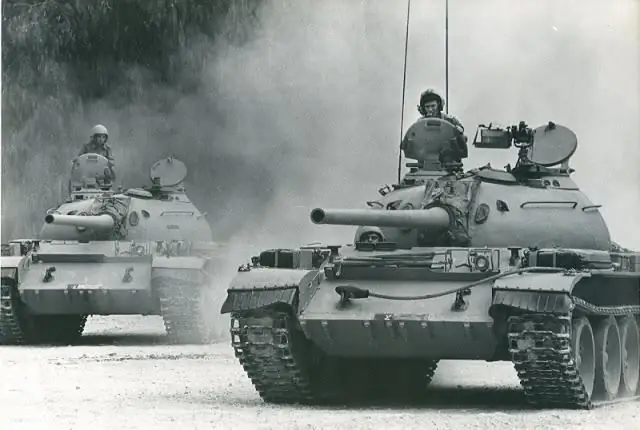
Harvoin taisteluajoneuvolla on aktiivinen ja pitkä käyttöikä. Neuvostoliiton keskikokoinen tankki T-54 on juuri sellainen harvinaisuus. Se syntyi toisen maailmansodan vuosina, palveli koko kylmän sodan ajan, taisteli monissa kuumissa pisteissä ja on edelleen monien maailman osav altioiden riveissä. Mikä on tällaisen säiliön pitkäikäisyyden salaisuus?